DRAG DROP (Drag and Drop is not supported)
You are a field service administrator for your company.
You review the Field Service administrator guide to understand how the status fields can support your company’s business processes.
Which unique entity system status value matches with its Entity Type? To answer, drag the appropriate unique entity system status values to the appropriate Entity Type. Each unique entity system status value may be used once, more than once, or not at all. You may need to drag the split bar between panes or scroll to view the content.
NOTE: Each correct selection is worth one point.
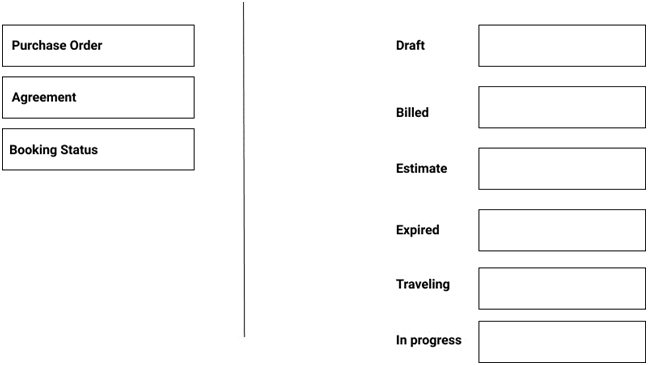
- See Explanation section for answer.
Answer(s): A
Explanation:
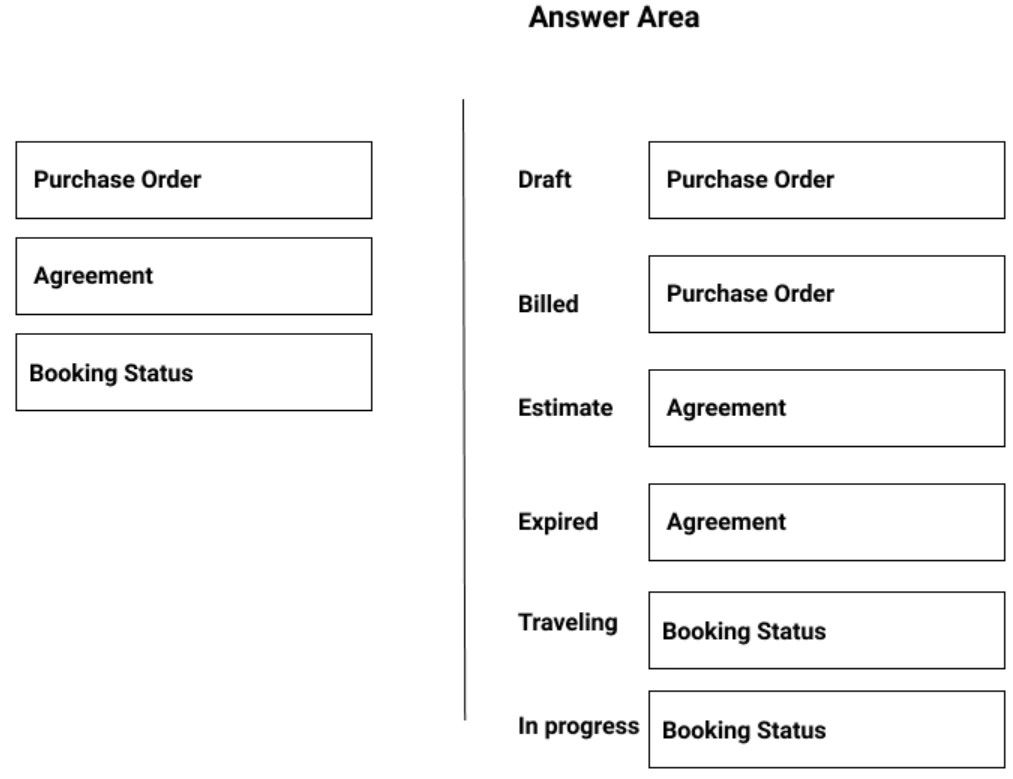
Reveal Solution Next Question